HCR-12A
Payload 12kg, Reach 1300mm The Collaborative robot HCR-12A is most effective in automotive, logistics or metal processing industries, which deal with heavy products. If you apply HCR-12A to repetitive and dangerous tasks such as loading & unloading metal materials into the machine, you can make your working environment safer and improve productivity.

Strong at
Palletizing
Mobile Welding
General Pick & Place
CNC Machine Tending
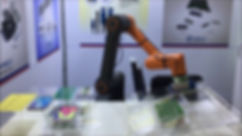
EASY
MODULAR COMPONENTS ALLOW EASY REPAIR BASED ON ONLY THE USER MANUAL
The spare parts of HCR-12A are all of modular design, so there is no need to call in an engineer. Repair the robot yourself throughout the product life cycle and cut your operating expenses.
A HALF-DAY TRAINING IS SUFFICIENT FOR PROGRAMMING THE ROBOT
--- EVEN FOR INEXPERIENCED OPERATORS
HCR-12A operates with a tablet-style pendant that features ergonomic wrist support. It's as simple to use as your average smartphone. The teach pendant allows users to monitor the work flow intuitively through icons and on a timeline basis. HCR-12A supports real-time, on-screen 3-D monitoring & play-back of the programmed task, making it possible for new operators to view their completed program prior to deployment. Should they desire, operators can even move the robot manually with their hands to desired way-points and let the robot memorize the new movement. This direct teaching function makes it even easier for more inexperienced operators to order a job.
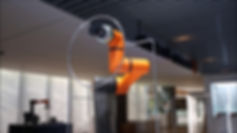
FLEXIBLE
NEED THE SUPPORT OF TWO ROBOTS? OPERATE BOTH WITH A SINGLE CONTROLLER
A single control box can operate two robots at the same time, reducing initial investment in controllers. Two robots use one teach pendant to be operated as two separate units.
ALTERATION TO PRODUCTION LAYOUT DOES NOT REQUIRE
A NEW ROBOT OR PROGRAM
HCR-12A is easily re-deployable thanks to its simple programming, and without the need for a safety cage, it's also space-saving. Simply add or move the robot to/around your production line without having to make changes to its programming. In addition, two I/O modules and EtherCAT socket are located at the tip of the robot body, allowing easy connection to various peripherals - such as a gripper, vision sensor, and/or suction to suit your diverse tasks.
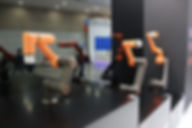
SAFE
LEAVE THE DANGEROUS TASKS TO THE ROBOT
Deploy HCR-12A for tasks with a high risk of burns or caught-in-between incidents - such as injection molding, press, and CNC. This will help to prevent serious accidental injuries during the operation, improving the work environment.
REMAIN SAFE WORKING DIRECTLY WITH THE COBOT
Hanwha Robotics' HCR-12A is set up with a virtual safety boundary that can be configured and customized according to the specific needs of your work environment. HCR-12A is programmed to automatically stop operation upon sensing the smallest shock, making it possible for the robot to work side-by-side with robotics operators without a safety fence. This helps you to avoid collisions in advance and to keep your business a safe workplace.